Custom Injection Molding Companies: Innovating Your Production Process
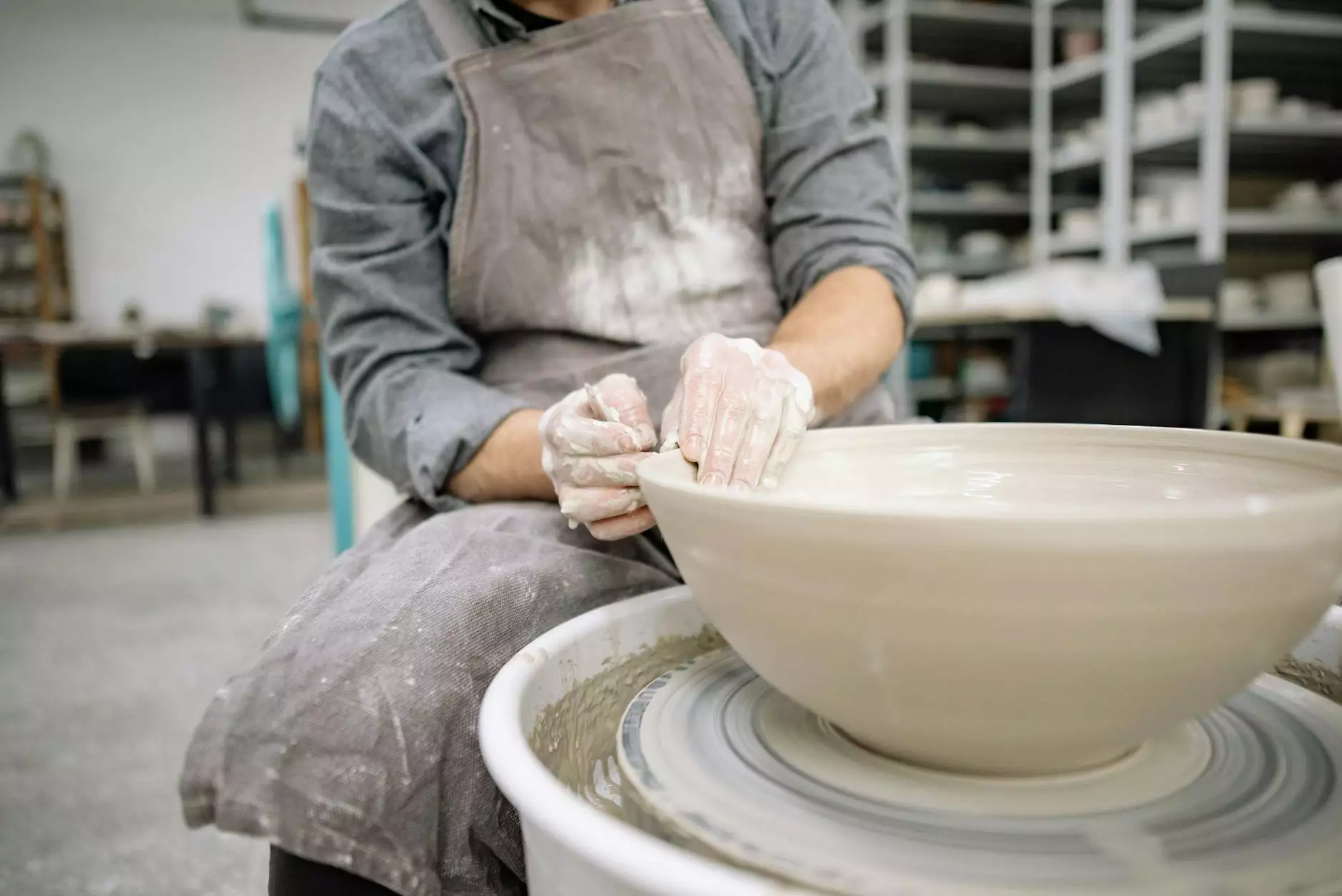
In today’s fast-paced manufacturing landscape, the role of custom injection molding companies cannot be overstated. These companies revolutionize the way products are designed, manufactured, and delivered, providing businesses with unparalleled efficiency and innovation in creating high-quality plastic parts. This article delves into the intricacies of the custom injection molding industry, discussing its benefits, applications, and how to choose the right partner for your specific needs.
Understanding Custom Injection Molding
Custom injection molding is a manufacturing process that involves injecting molten material into a mold to create specific shapes and forms. This process is highly versatile and is used to produce a wide range of products, from simple components to complex assemblies. The following steps outline the injection molding process:
- Material Selection: The appropriate material, usually thermoplastic or thermosetting polymers, is chosen based on the requirements of the final product.
- Mold Design: A specialized mold is designed and created based on the specifications of the intended product.
- Injection Process: The selected material is heated until it becomes molten and is injected into the mold under high pressure.
- Cooling and Solidifying: The molten material cools and solidifies within the mold, taking its shape.
- ejection: Once solidified, the mold opens, and the finished part is ejected.
Benefits of Working with Custom Injection Molding Companies
Engaging with custom injection molding companies offers numerous advantages, making it an attractive option for businesses looking to optimize their production processes:
1. Cost-Effectiveness
One of the primary benefits of injection molding is its cost efficiency, especially when producing high volumes of parts. The initial investment in mold creation can be significant; however, once the mold is produced, the cost per unit decreases dramatically with larger production runs.
2. High Precision and Consistency
Injection molding ensures that each part produced is uniform and meets exact specifications. Advanced technology employed by custom injection molding companies allows for precise control over the molding process, reducing variations and enhancing quality.
3. Speed and Efficiency
The injection molding process is remarkably efficient and can produce thousands of parts in a short timeframe. This rapid production capability allows companies to meet tight deadlines and respond effectively to market demands.
4. Versatility in Material Choices
Custom injection molding companies offer a broad range of materials to choose from, including various plastics, elastomers, and metals. This versatility allows businesses to select the right material for their product's functional requirements and aesthetic preferences.
5. Reduced Waste
The injection molding process is inherently efficient, resulting in minimal material waste compared to other manufacturing methods. Any leftover scrap can often be reprocessed and reused, further enhancing sustainability.
Applications of Custom Injection Molding
Custom injection molding is used across a wide array of industries due to its adaptability and efficiency. Below are some key sectors that rely on this manufacturing method:
- Automotive: Custom injection molding produces various components like dashboards, interior trim, and fuel tanks.
- Consumer Products: Products such as toys, kitchen utensils, and personal care items often utilize injection-molded parts for better reliability and design.
- Medical Devices: The medical industry benefits from high-precision injection molding to create components for instruments, syringes, and housings for diagnostic equipment.
- Electronics: Many electronic devices use injection-molded plastic casings, connectors, and other components critical to functionality and durability.
- Aerospace: The aerospace industry employs injection molding for lightweight and durable components that meet stringent regulations and safety standards.
Choosing the Right Custom Injection Molding Company
Selecting the right partner among custom injection molding companies is crucial for the success of your project. Here are several factors to consider when making your choice:
1. Experience and Expertise
Look for a company that has extensive experience in the specific industry relevant to your project. An established firm will have the knowledge and skills to navigate potential challenges and optimize production.
2. Technology and Equipment
Evaluate the technology and machinery used by potential partners. Advanced equipment enhances precision and efficiency, reducing lead times and improving the quality of the molded products.
3. Quality Assurance Processes
Inquire about the quality control measures implemented by the custom injection molding companies. A rigorous quality assurance process helps ensure that every part produced adheres to necessary standards and specifications.
4. Communication and Support
Effective communication is vital throughout the production process. Choose a company that values open lines of communication and provides ongoing support to address any concerns or adjustments needed along the way.
5. Pricing Transparency
Ensure that the company offers clear pricing with no hidden fees. A reliable partner provides detailed quotes and outlines all associated costs involved in the custom injection molding process.
Future Trends in Custom Injection Molding
The custom injection molding industry is continuously evolving. Some of the anticipated trends that could shape the future include:
- Automation and Smart Manufacturing: Increased automation will likely improve efficiency and lower costs with the use of AI and IoT technologies.
- 3D Printing Integration: The integration of 3D printing may reshape mold design and manufacturing processes, enhancing design flexibility and reducing time to market.
- Sustainability Initiatives: With growing environmental awareness, the use of biodegradable plastics and recycled materials will become more prevalent.
- Customization and Personalization: As consumer preferences lean towards personalized products, custom injection molding companies will need to adapt their processes to meet these demands.
Conclusion: Partnering for Success
In summary, custom injection molding companies are indispensable allies in the quest for innovative and cost-effective production solutions. Their capacity to produce highly precise components with diverse material options and rapid turnaround times empowers businesses across various sectors. By carefully selecting a partner and leveraging the benefits of this manufacturing method, businesses can enhance their market position and drive growth in a highly competitive landscape.
For businesses looking to explore the possibilities offered by custom injection molding, it is vital to collaborate with a reputable company that understands their specific needs. Consider reaching out to industry leaders like Deep Mould at deepmould.net to learn more about how they can assist you in achieving your manufacturing goals.