Exploring the Precision CNC Machining Factory Landscape
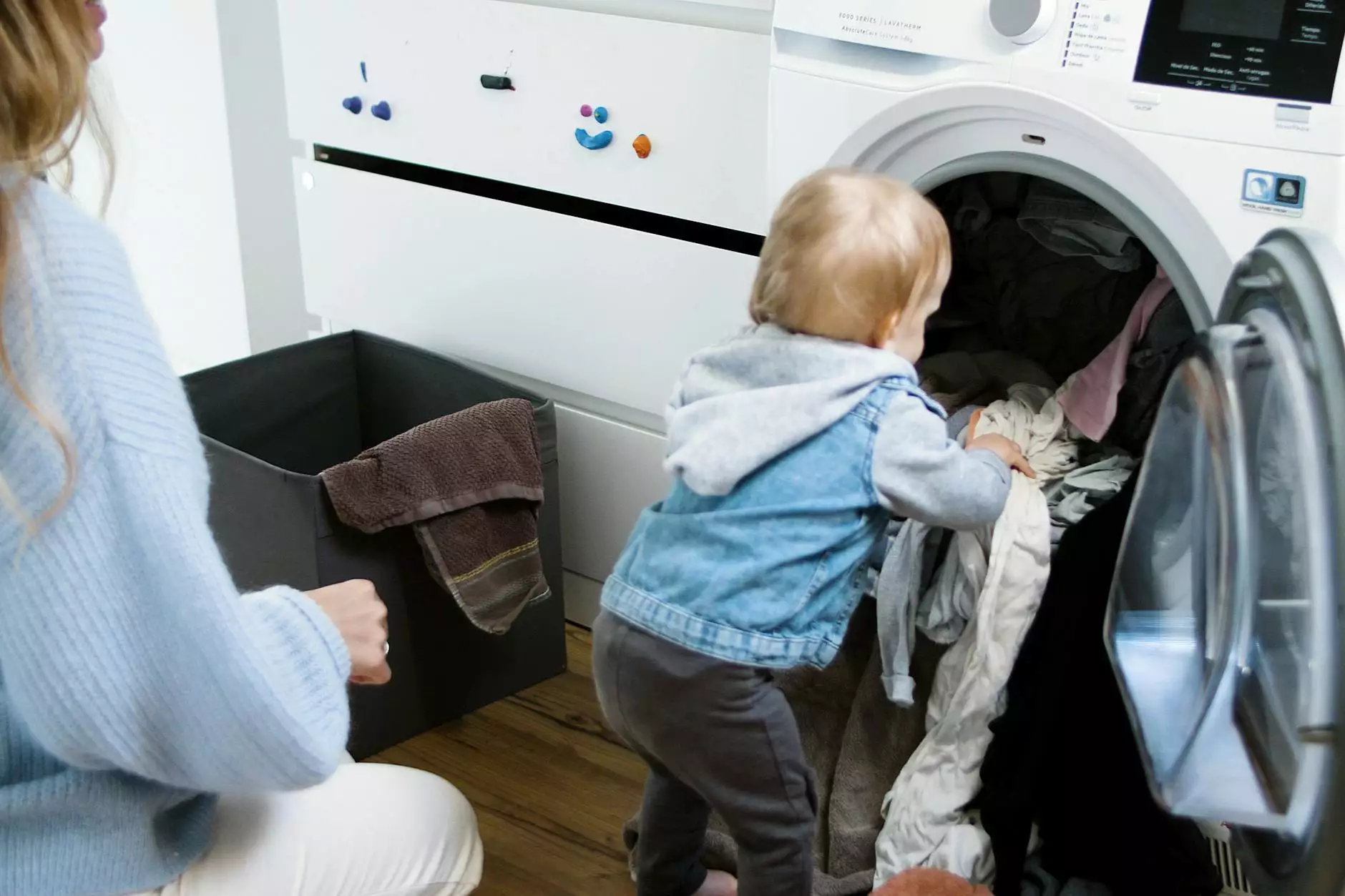
In today's rapidly evolving manufacturing environment, the term precision CNC machining factory has become increasingly significant. As industries expand and the demand for customized components rises, precision machining stands out as a cornerstone of modern manufacturing. This article delves deep into the intricacies of precision CNC machining, highlighting its processes, advantages, and factors to consider when selecting a machining partner.
Understanding CNC Machining
CNC, or Computer Numerical Control, machining is a technique that uses computers to control machine tools. This kind of automation in manufacturing enables the production of complex parts with high levels of accuracy and repeatability.
How Does CNC Machining Work?
The process begins with creating a 2D or 3D design using CAD (Computer-Aided Design) software. This design is then converted into a numerical code by CAM (Computer-Aided Manufacturing) software. The CNC machine interprets this code, controlling tools such as lathes, mills, and routers to remove material and create the desired shape.
The Role of Precision in CNC Machining
Precision is key in CNC machining. The term “precision” refers to the ability of the machining process to produce components with minimal deviation from specifications. This is crucial in industries such as aerospace, automotive, and medical, where even the slightest error can have serious repercussions.
Benefits of Precision CNC Machining
Choosing a precision CNC machining factory can offer numerous advantages, including:
- High Accuracy and Consistency: CNC machines can achieve tight tolerances, which leads to parts that meet exact specifications every time.
- Efficiency: Once a design is programmed, CNC machines can produce large quantities of parts with minimal human intervention, drastically reducing production time.
- Complex Geometries: CNC machining can easily produce intricate designs that would be incredibly challenging or impossible with traditional machining methods.
- Material Versatility: CNC machines can work with a variety of materials, including metals, plastics, and composites, allowing for diverse application across industries.
Common Processes in a Precision CNC Machining Factory
1. Turning
Turning is a process where a cutting tool removes material from a rotating workpiece to create cylindrical parts. This is commonly used in producing shafts, rods, and other rotationally symmetric components.
2. Milling
Milling involves the use of rotating tools to remove material from a stationary workpiece. This method is versatile and can produce a variety of shapes including flat surfaces, slots, and complex profiles.
3. Drilling
This process creates holes in the workpiece. CNC drilling machines are programmed to accurately produce holes of varying diameters and depths.
4. Grinding
Grinding is a finishing process that uses an abrasive wheel to achieve the desired surface finish and precision measurements.
Factors to Consider When Choosing a Precision CNC Machining Factory
1. Experience and Expertise
Look for a machining factory with a proven track record in the industry. The more experienced a factory is, the better equipped they are to handle complex requirements and variations in designs.
2. Technology and Equipment
The technology and machinery used by the factory are crucial. Modern CNC machines with advanced capabilities can enhance precision and efficiency.
3. Quality Control
A reliable precision CNC machining factory will have stringent quality control measures in place to ensure that every component meets the required specifications through inspections and testing.
4. Customer Service
Effective communication and customer support are essential for a fruitful partnership. A factory that values customer service will provide updates, feedback, and assistance throughout the production process.
5. Production Capabilities
Evaluate the production capabilities of the factory. Can they handle high volume orders? What is their lead time? Understanding their capacity can help in planning and meeting deadlines.
Future Trends in Precision CNC Machining
As technology advances, the field of CNC machining continues to evolve. Here are some anticipated trends:
- Integration of AI: Artificial Intelligence is set to enhance the efficiency of CNC machines, making them smarter and more adaptive.
- Increased Automation: The use of robotics for loading and unloading parts will improve productivity and reduce labor costs.
- 3D Printing Synergy: Combining traditional CNC machining with 3D printing technology to create complex parts that are lightweight and strong.
- Sustainability Practices: Companies are moving towards sustainable processes, using recyclable materials and minimizing waste during production.
Conclusion: Elevate Your Manufacturing with Precision CNC Machining
Operating in the competitive landscape of metal fabrication demands excellence, and a precision CNC machining factory stands out as a critical partner in achieving that. By leveraging advanced technology, skilled expertise, and a commitment to quality, businesses can not only meet but exceed their manufacturing goals.
As you consider your next project, remember the benefits that high-quality precision machining can provide. Whether you’re in aerospace, automotive, or another industry that relies on precise components, selecting the right precision CNC machining factory like DeepMould.net could be the key to your success. Embrace the future of manufacturing, and watch your business transform through precision and innovation.