Understanding Rapid Prototyping Manufacturing in Metal Fabrication
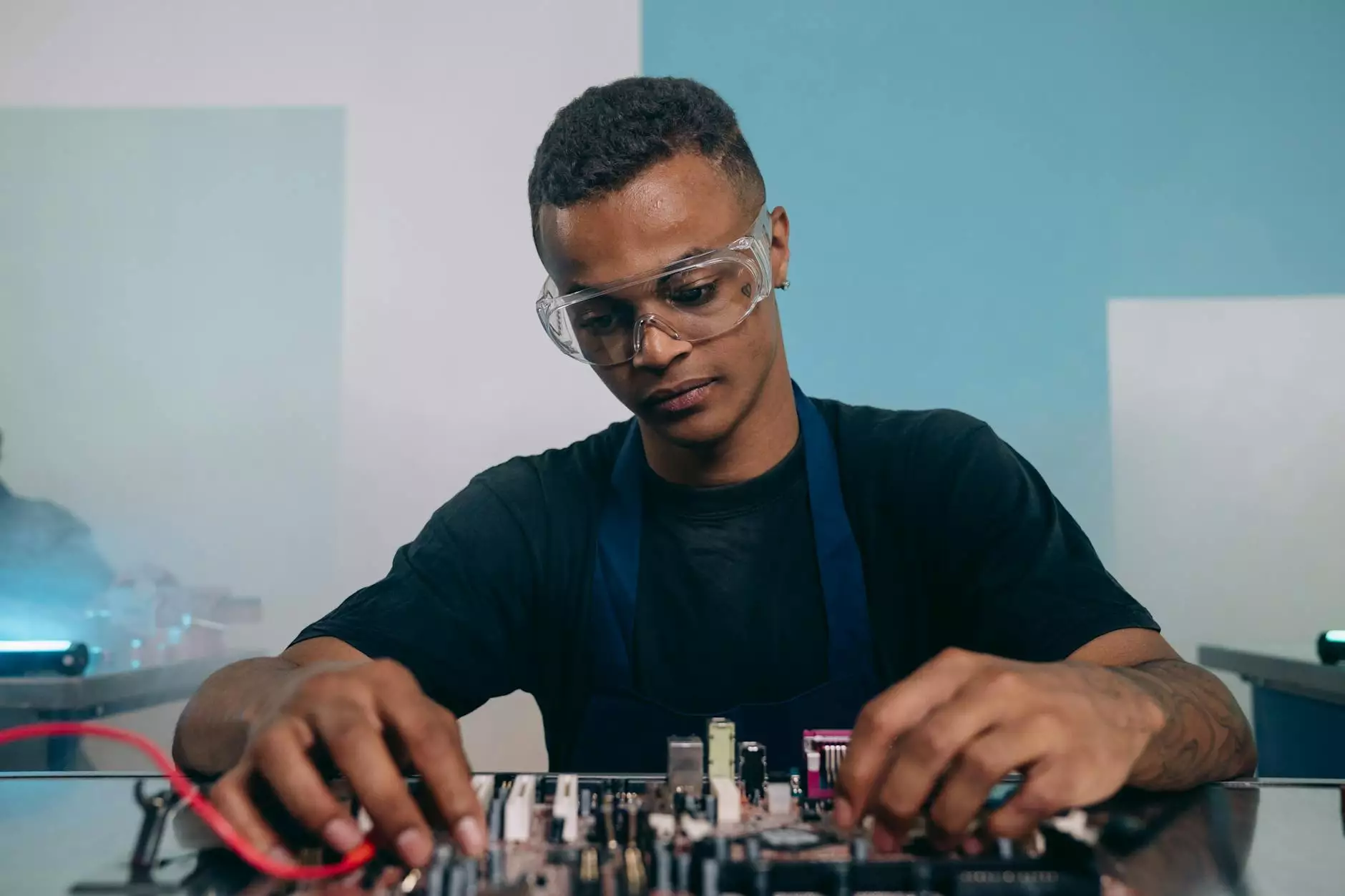
In the evolving landscape of manufacturing, businesses are constantly seeking ways to enhance their production processes, reduce costs, and deliver superior products. One innovative technique that has transformed the industry is rapid prototyping manufacturing. This method allows for the quick creation of prototypes, facilitating design iterations and ensuring the production of high-quality final products. In this article, we delve deep into the world of rapid prototyping manufacturing, particularly in the context of metal fabrication.
What is Rapid Prototyping Manufacturing?
Rapid prototyping manufacturing refers to a set of techniques used to fabricate a scale model of a physical part or assembly using three-dimensional computer-aided design (CAD) data. It is a process that enables designers and engineers to create models swiftly, which can dramatically accelerate the development cycle of a product. This approach is particularly crucial in industries where time-to-market is a significant competitive factor.
Key Technologies in Rapid Prototyping
The term rapid prototyping manufacturing encompasses several advanced technologies, each with its unique advantages. Some of the most prominent techniques include:
- 3D Printing (Additive Manufacturing): This method builds objects layer by layer from a digital model, allowing for complex geometries and designs.
- Stereolithography (SLA): A form of 3D printing that uses UV light to cure resins, resulting in highly detailed and smooth finishes.
- Selective Laser Sintering (SLS): A process that employs lasers to fuse powdered materials, ideal for creating functional parts and prototypes from various materials, including metals.
- Computer Numerical Control (CNC) Machining: While technically not rapid prototyping in the traditional sense, CNC milling and turning can rapidly produce prototypes from pre-existing designs with high precision.
Benefits of Rapid Prototyping in Metal Fabrication
When it comes to metal fabrication, the implementation of rapid prototyping can yield substantial benefits, including:
- Enhanced Design Flexibility: Engineers can quickly test and modify prototypes, allowing for iterative design improvements before full-scale production begins.
- Cost-Effective Solutions: By identifying design flaws early in the process, businesses can save money that might otherwise be spent on rework or scrap materials.
- Faster Time-to-Market: Rapid prototyping enables companies to bring their products to market faster, providing a significant edge in competitive industries.
- Increased Collaboration: Prototypes can be shared among teams and stakeholders for feedback, fostering a collaborative environment where ideas can be refined and enhanced.
- Testing and Validation: Prototypes allow for thorough testing, ensuring that materials and designs meet specific performance criteria before mass production.
The Process of Rapid Prototyping Manufacturing
Understanding the process of rapid prototyping manufacturing is crucial for anyone looking to leverage this technology in metal fabrication. The general steps involved include:
1. Conceptualization and Design
The process begins with the creation of a detailed design. Engineers utilize CAD software to develop digital models that represent the desired final product. These models must account for material properties, tolerances, and functional requirements.
2. Select the Prototyping Technology
Depending on the complexity and requirements of the design, the right prototyping technology is chosen. This decision can significantly influence the quality, durability, and cost of the final prototype. For metal parts, methods like SLS or CNC machining are often preferred.
3. Prototype Fabrication
Once the technology is selected, the prototype is fabricated. This step involves the layering of materials if using additive methods, or the cutting and milling in CNC machining. The focus is on achieving a high degree of accuracy to ensure the prototype closely resembles the intended design.
4. Post-Processing
After the initial fabrication, many prototypes undergo post-processing, which can include sanding, coating, or heat treatment. This enhances the aesthetic and functional properties of the prototype, making it closer to the final product.
5. Testing and Evaluation
The finalized prototype is then subjected to extensive testing. This can involve stress tests, functional tests, and validation against design specifications. The aim is to identify any issues before full production starts.
Applications of Rapid Prototyping in Metal Fabrication
The versatility of rapid prototyping manufacturing allows for its application across various industries. Some notable applications include:
- Aerospace Industry: Rapid prototyping is used to create lightweight components that enhance fuel efficiency while maintaining safety standards.
- Automotive Sector: Manufacturers utilize prototyping to develop custom parts that can undergo rigorous testing before entering production.
- Medical Devices: The capability to rapidly prototype can lead to innovative medical solutions tailored to specific patient needs.
- Consumer Electronics: Rapid prototyping allows electronic companies to create functional designs that meet both aesthetic and ergonomic demands.
The Future of Rapid Prototyping Manufacturing
The future of rapid prototyping manufacturing is promising, with ongoing advancements and research leading to new capabilities. Innovations such as multi-material printing, enhanced software for simulations, and improved materials are poised to make prototyping even more efficient and accessible. As industries continue to face pressures for rapid innovation and cost-effectiveness, rapid prototyping will play a pivotal role in meeting these challenges.
Conclusion
In conclusion, rapid prototyping manufacturing represents a groundbreaking shift in the way products are developed in the field of metal fabrication. Its ability to streamline processes, promote collaboration, and reduce time and costs are invaluable to businesses striving for excellence in today’s competitive market. By adopting rapid prototyping technologies, companies can not only enhance their product development cycles but also ensure they remain at the forefront of industry innovation.